25kW电动汽车SiC直流快充设计指南:经验总结 (电动汽车几千瓦)
整理分享25kW电动汽车SiC直流快充设计指南:经验总结 (电动汽车几千瓦),希望有所帮助,仅作参考,欢迎阅读内容。
内容相关其他词:25kW电动汽车SiC直流快充设计指南:经验总结,25kW电动汽车SiC直流快充设计指南:经验总结,150kw电动汽车,电动汽车52kwh,25kW电动汽车SiC直流快充设计指南,电动汽车20kwh什么意思,25kW电动汽车SiC直流快充设计指南,25kW电动汽车SiC直流快充设计指南:经验总结,内容如对您有帮助,希望把内容链接给更多的朋友!
图kW电动汽车直流充电桩的高级框图在任何电源转换器设计过程中,都必须实施硬件保护,这一点很重要。事实上,功率开关器件是转换器的核心,设计人员需要在确保*在各种特定的场景中提供保护功能。在这些场景下,过压和过流保护是基本要求。这两种保护可以采用多种方法实现:相对简单的方法,例如在关键回路添加阻容元件,形成所谓的缓冲器(Snubber),有助于*电压峰值;另一种较为复杂的方法,就是在瞬时条件超过预定标准时,阻断器件运行。采用这种方法时,比如我们在开发双有源桥式转换器时采用了这种方法,在转换器的两侧添加具有指定阈值和迟滞的电压比较器来实现过压保护,在DC-Link过压时阻断栅极驱动器。类似的方法也适用于过流保护解决方案。利用自带过流保护功能的栅极驱动器就可以方便地解决问题。使用具有去饱和保护(DESAT)功能的NDC栅极驱动器,可降低BOM成本并提高产品市场竞争力。在下一部分中,我们将介绍在硬件启动测试阶段进行的PFC级和DABDCDC级DESAT阈值的测量和评估,这在控制固件(FW)调试之前是必不可少的。在DABDC-DC级,我们则着重于增强DESAT保护功能,以实现宽输出(V至V)工作电压范围。全数控电源转换器中的关键硬件功能是硬件保护、过流和过压保护,旨在防止功率半导体器件在过流或短路期间消耗过大的功率。这可以防止出现过压尖峰,避免损坏功率半导体。硬件保护在控制算法启动和调试阶段至关重要,因为此时经常会发生不可预测的MOSFET开关,会导致功率器件烧毁,而需要消耗时间和成本进行处理,非常麻烦。PFC级DESAT保护PFC级中使用的NCD隔离式栅极驱动器具有DESAT保护功能,有助于对所用的PIMSiCMOSFET进行过流保护设计。“kWSiC直流快充设计指南(第六部分):用于电源模块的栅极驱动*”描述了设计过程。我们在硬件启动阶段评估了DESAT功能,并测量了DESAT动作阈值电流和SiCMOSFET软关断时间。用于高压侧SiCMOSFET的DESAT动作电流评估的测量原理如图2所示;左边是高压侧、右边是低压侧SiCMOSFET测量。我们选择了与应用的DC-LinkDC-Link电压相同的测试电压,即V。通过栅极测试脉冲导通待测高压侧SiC模块,使DESAT保护动作。假设直流电阻可以忽略不计,所以流经待测SiCMOSFET的电流上升di/dt仅受μH的串联PFC电感的*。电流上升可由下式表示。图2PFC级DESAT动作电流硬件启动测试高压侧SiCMOSFET(左)和低压SiCMOSFET(右)在“kWSiC直流快充设计指南(第六部分):用于电源模块的栅极驱动*”中,针对VDC-LinkDC-Link电压,我们计算出DESAT阈值电流理论值为÷A;应用手册AND对计算过程进行了详细阐述,测量在°C室温下进行。需要注意的是,DESAT阈值水平还取决于SiCMOSFET、栅极驱动器和DESAT保护电路中元件的温度。根据图3中的测量结果,SiCMOSFET的导通时间为至ns,软关断时间为至ns(当DESAT工作时)。高压侧DESAT动作阈值的测量值为A,低压侧为A。我们评估了所有原型设计并测量了DESAT阈值,得出A-.7A的范围。由于PFC级在.5kW(1.5kW是kWPFC级的功率裕度)和VRMS时的最大相电流应为A,因此我们将PFC级中的DESAT阈值提高了%,以便在A-A范围内的最小电流阈值下激活。对于商用量产产品,进行评估说明必不可少,应使用足够的样本进行测量,以便对所用电子元件的数值公差引起的变化进行可靠评估。图3DESAT跳闸电平测量高压侧(左)和低压侧(右)SiCMOSFET为了解环境温度对DESAT电流阈值水平的影响,我们在°C和°C下对同一样品进行测量;DESAT动作阈值增加了5.4A。在两种温度条件下的测量结果如图4所示。这一测量结果表明,针对整个工作电压范围和整个温度范围设计DESAT保护是多么重要。图℃(左)和℃(右)下的DESAT动作电流备注:图2中的测试仅评估了一个SiCMOSFET发生短路故障时的动作电平;该测试并未评估电流从高压侧流向低压侧SiCMOSFET时的上下桥臂短路情形。发生桥臂短路时,电流不再受到*。DESAT保护不能有效地保护SiCMOSFET,因为主要*因素(即串联的PFC电感)*了电流上升,如公式(1)所示,从而允许DESAT在所需电流水平下作出反应,避免大电流继续流过MOSFET。DABDCDC级的DESAT保护增强与PFC级相同,双有源桥转换器DCDC级也使用了具有DESAT保护功能的NDC栅极驱动器。原理上来说,这种保护利用电源路径端子两端不断改变的压降来监控流过驱动开关器件的电流水平。当然,必须了解开关器件的特性才能进行正确的过流保护配置。虽然数据手册提供了基本信息,但通常不会很详细并且贴合应用案例,因此无法准确选择器件。样机测试固然重要,电路*工具在设计过程中也很有帮助。如图5的部分电路图所示,建议的驱动电路遵循NCD数据手册建议。图5NCD栅极驱动电路图尽管计算去饱和阈值电阻(图5中的RA)看似简单,但却未必如此,因为RDS,ON参数并不是恒定的;它随栅极电压以及流经器件的瞬时电流而变化。根据器件数据手册中提供的数据,而简单地将这两个关联项结合起来,以获得实际RDS值,并用于RDESAT值计算,这并非一项简单的任务。若有器件*模型会更容易实现。由于NCD的完整*模型尚未公布,我们建立了其去饱和功能的简化模型,该模型可与开关器件结合使用。*结果显示,DESAT静态阈值取决于电阻R1。原边半桥的电阻初选原边.3kΩ,副边副边半桥阻值选择.3kΩ,因为在某些条件下,副边副边电流会稍高一些。图6所示为*栅极电路图。图6NCD栅极驱动器*电路图图7显示了不同R1电阻值下*得到的DABDESAT保护静态阈值。图7不同R1下*得到的DABDESAT保护静态阈值与PFC级一样,DABDCDC级的去饱和保护也得到了验证。下图为两侧功率级的简化示意图,包含功率电感和变压器。图8两侧功率级的简化图,包含功率电感和功率变压器可能的故障条件数相对较多。因此,我们为去饱和保护测试选择了以下可能的情况,以*测试次数,确保设置简单且可重现:•原边原边开关——副边副边短路*(图9)图9副边短路*副边•副边副边开关–原边短路*原边(图)图原边短路*原边在测试期间,所有开关均保持关断状态,除了待测开关。理想情况下,需要能够产生单脉冲的专用测试软件。如果没有测试软件,可以考虑选择最小开关频率大约1kHz的,具有产生长脉冲的占空比(推荐范围>-μs)。脉冲必须足够长,以使待测开关所经受的DC-LinkDC-Link电压和有效电感的特定组合能够在一个脉冲内达到预期的去饱和电流阈值。通过假定所选测试电压(正常工作电压)、DESAT保护动作时的峰值电流,以及变压器的漏感和原边串联谐振电感,就可以通过公式(1)计算所需时间。图所示为的DAB原边测量的典型波形如图所示。图原边原边DABDESAT阈值测量RA(图5).3kΩDC-LinkDC-Link为V时,最大电流达到A,而DC-LinkDC-LinkV时,该电流高达.1A。这似乎有点奇怪,因为静态阈值*显示当Rdesat=.3kΩ时,动作电流为.9A。不仅如此,V和V下达到的最大电流还存在相当大的差异。可以通过增加设置电阻来降低DESAT动作阈值。因此,将Rdesat.3kΩ增加到kΩ后重新测量:图原级原边DABDESAT阈值测量RA(图5)kΩ出乎意料的是,2种电压下的最大阈值电流与预期不同;电流本应下降大约A,但实际在V时下降了8A,在V时增加了4A,高达.9A。副边副边的情况似乎更糟,一旦原边原边短路,其有效电路电感会更低些。如图所示,V时最大电流达到.6A,其中Rdesat设置为.2kΩ。因此,未在V和V下进行测试。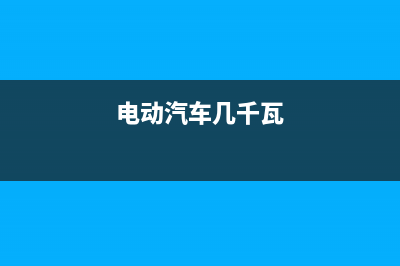