MCU解决800V电动汽车牵引逆变器的常见设计挑战的3种方式 (mcu电机控制器作用)
整理分享MCU解决800V电动汽车牵引逆变器的常见设计挑战的3种方式 (mcu电机控制器作用),希望有所帮助,仅作参考,欢迎阅读内容。
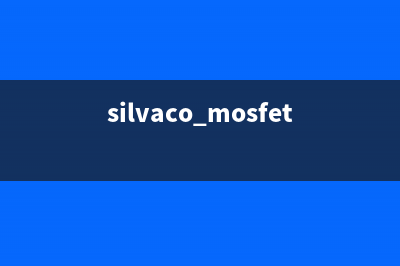
内容相关其他词:mcu801a,mcu电机控制,电车mcu故障,mcu上电,mcu电机控制器说明书,mcu1000,mcu电机控制器说明书,mcu 电机,内容如对您有帮助,希望把内容链接给更多的朋友!
●快速充电–在相同的电流下提供双倍的功率。●通过利用碳化硅(SiC)提高效率和功率密度。●通过使用更细的电缆减少相同额定功率下V电压所需的电流,从而减轻重量。在牵引逆变器中,微*(MCU)是*的大脑,通过模数转换器(ADC)进行电机控制、电压和电流采样,使用磁芯计算磁场定向控制(FOC)算法,并使用脉宽调制(PWM)信号驱动功率场效应晶体管(FET)。对于MCU,向V牵引逆变器的转变对其带来了三个挑战:●更低延迟的实时控制性能需求。●增加了功能安全要求。●需要快速响应*故障。在本文中,我们将讨论基于Arm®的Sitara™AM-Q1和C™MCU等器件如何应对这些挑战。更低延迟的实时控制为了控制牵引电机的扭矩和速度,MCU使用外设(ADC、PWM)和计算内核的组合来完成控制环路。随着转向V*,牵引逆变器也转向宽带隙半导体(例如SiC),因为它们在V时大大提高了效率和功率密度。为了实现SiC所需的更高开关频率,这种控制环路延迟成为优先事项。低延迟控制环路还使工程师能够以更高的转速运行电机,从而减小电机的尺寸和减轻重量。要了解并缩短控制环路延迟,您必须了解控制环路信号链及其各个阶段,如图1所示。图1:控制环路信号链为获得出色的实时控制性能,您必须优化整个信号链,包括硬件和软件。从ADC采样(来自电机的输入)到写入PWM(输出以控制电机)所花费的时间是实时控制性能的基本衡量标准。从ADC采样开始,逆变器*需要准确快速的采样,即实现高采样率、至少位分辨率和低转换时间。一旦可进行采样,它需要通过互连传输到处理器并由处理器读取,并优化的总线和内存访问架构缩短延迟。在处理器中,内核需要使用FOC算法根据电机的相电流、速度和位置计算下一个PWM步骤。为了更大限度地减少计算时间,内核需要较高的时钟速率并且必须高效地执行特定数量的指令。此外,内核需要执行一系列指令类型,包括浮点、三角和整数数学指令。最后,内核再次使用低延迟路径将更新后的占空比写入PWM发生器。在PWM输出上应用死区补偿将防止在切换高侧和低侧FET时发生短路,最好在硬件级别应用以减少软件开销。TIMCU的牵引逆变器控制环路延迟低至2.5µs,AM-Q1的延迟小于4µs。这种级别的控制环路延迟将面向包括SiC架构的未来设计,。增加功能安全要求由于牵引逆变器提供电力来控制电机,因此它们本质上是功能安全型关键*。由于V*有可能提供更高的功率、扭矩、速度(或三者兼而有之),因此牵引*需要功能安全达到汽车安全完整性等级(ASIL)D级要求。功能安全*的一个关键部分是MCU,因为它需要智能地做出安全响应*故障的决策。因此,使用通过ASILD认证的MCU是一个重要的安全元素。为了让工程师更轻松地满足特定于牵引逆变器的*安全要求,TIMCU提供了额外的功能。例如,相电流反馈表示有关电机扭矩的信息,这使得这些信号对安全至关重要。因此,许多工程师更喜欢对相电流进行冗余采样,这意味着MCU必须具有多个*的ADC。快速响应*故障工程师面临的另一个挑战是在出现故障时能够快速将电机置于安全状态,例如续流。在AM-Q1器件中,故障通用输入(用于过流、过压或高速故障)会进入到创新的可编程实时单元(PRU)。在PRU中执行的固件可以正确评估和响应故障类型并执行所需的PWM保护序列,如图2所示,然后根据需要直接将PWM置于安全状态。这些*作发生在短短ns内。此外,由于固件是用户可进行编程的,因此工程师可以在必要时添加额外的自定义逻辑来满足他们的应用要求。图2:流程图显示了基于故障输入的PWM输出的预期保护行为随着越来越多电动汽车的生产,设计趋势将转向SiC和V技术,同时需要提高电机控制性能并满足牵引逆变器的功能安全要求。随着世界朝着电气化方向发展,性能和效率方面的创新对于帮助汽车工程师设计下一代电动汽车至关重要。其他资源●参阅应用手册“用于牵引逆变器的AMx”。●浏览用于实现电机控制环路的代码。标签: mcu电机控制器作用
本文链接地址:https://www.iopcc.com/jiadian/25207.html转载请保留说明!